Spiral Plate Heat Exchanger (SPHE) is a
industrial heat exchange equipment that adopts a spiral plate design and realizes heat transfer through the flow of fluid in a spiral channel. Due to its special structure, the spiral plate heat exchanger has significant advantages in handling fluids with high viscosity, easy scaling, and easy deposition, and is widely used in chemical, petroleum, pharmaceutical, food processing and other fields.
Structure of Spiral Plate Heat Exchanger
The spiral plate heat exchanger consists of two or more spiral plates, which are welded or clamped to form two flow channels for hot fluid and cold fluid to flow respectively. The fluid flows in the spiral channel between the plates, and the heat is transferred from one fluid to another through the plates.
Working Principle
1. Flow of hot and cold fluids: Spiral plate heat exchangers usually use countercurrent or countercurrent flow to increase heat exchange efficiency. The hot fluid and the cold fluid flow in different spiral channels respectively.
2. Heat transfer: The hot fluid transfers heat to the cold fluid through the spiral plate, causing the cold fluid temperature to rise and the hot fluid temperature to drop.
3. Fluid distribution: The spiral plate heat exchanger ensures that the fluid is evenly distributed throughout the spiral channel by designing different inlet and outlet ports to avoid fluid short circuit or uneven flow.
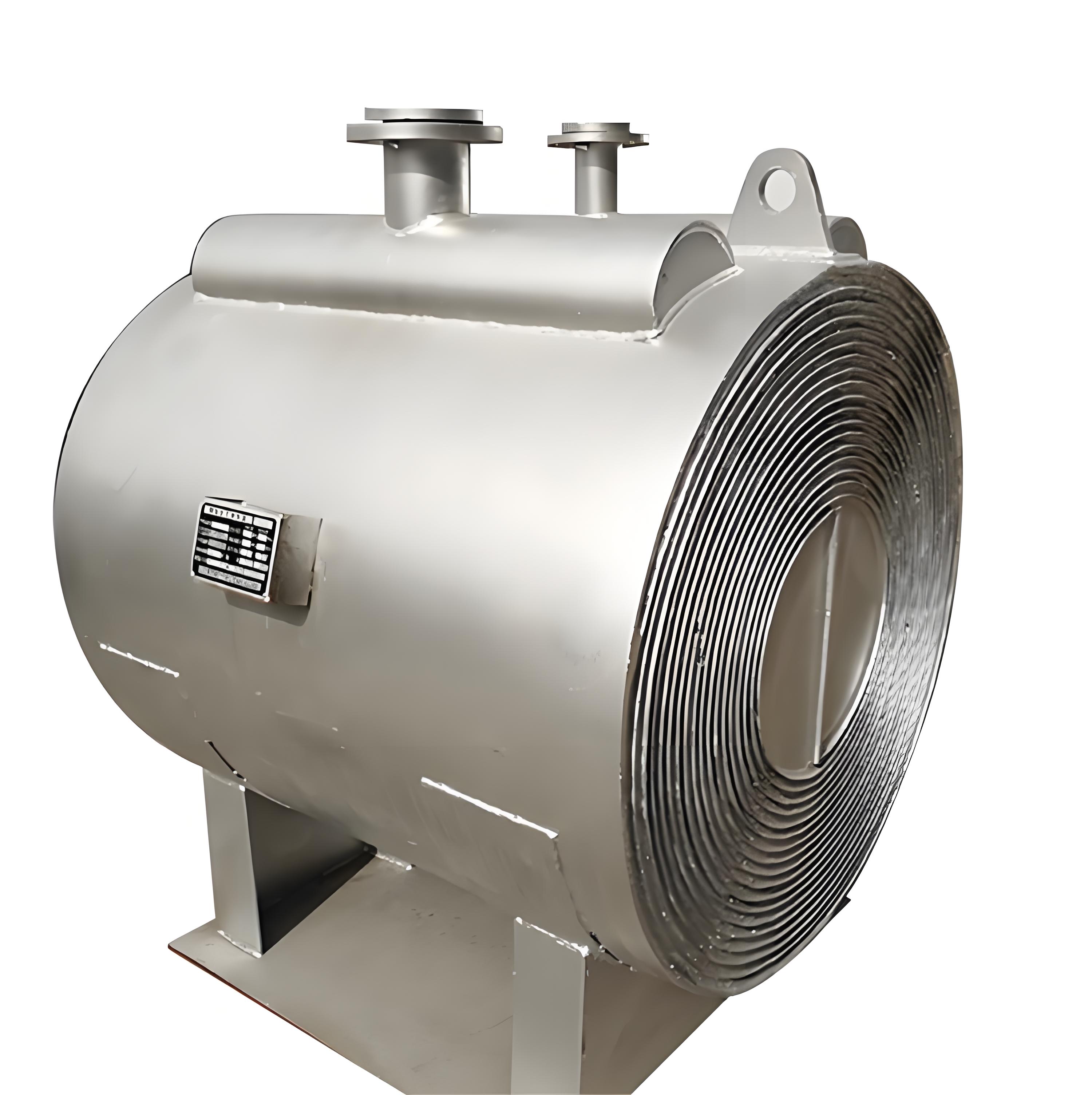
Key Features
This advanced heat exchanger comprises multiple spiral plates either welded or clamped together to create dual flow paths for hot and cold media. Its innovative design ensures that fluids move efficiently through spiral channels, maximizing heat transfer while minimizing energy loss. The ability to handle complex fluids and maintain consistent performance sets the SPHE apart from conventional heat exchangers.
Detailed Description
The working principle of the SPHE involves a countercurrent flow mechanism that enhances heat exchange efficiency. Hot and cold fluids traverse separate spiral channels, facilitating optimal thermal transfer. This process results in an elevated temperature for the cold fluid and a reduced temperature for the hot fluid. Furthermore, the SPHE employs strategically designed inlet and outlet ports to ensure uniform fluid distribution, preventing short circuits or uneven flow patterns. Its robust construction supports applications where traditional heat exchangers may struggle due to limitations in handling viscous or scaling-prone substances.
Applications
From chemical plants to pharmaceutical facilities, the SPHE finds utility in environments demanding reliable and efficient heat exchange solutions. Industries such as oil refining, food processing, and biotechnology benefit significantly from its capacity to manage diverse fluids under challenging conditions. Its adaptability makes it an ideal choice for scenarios requiring precise temperature control and maximum operational effectiveness.
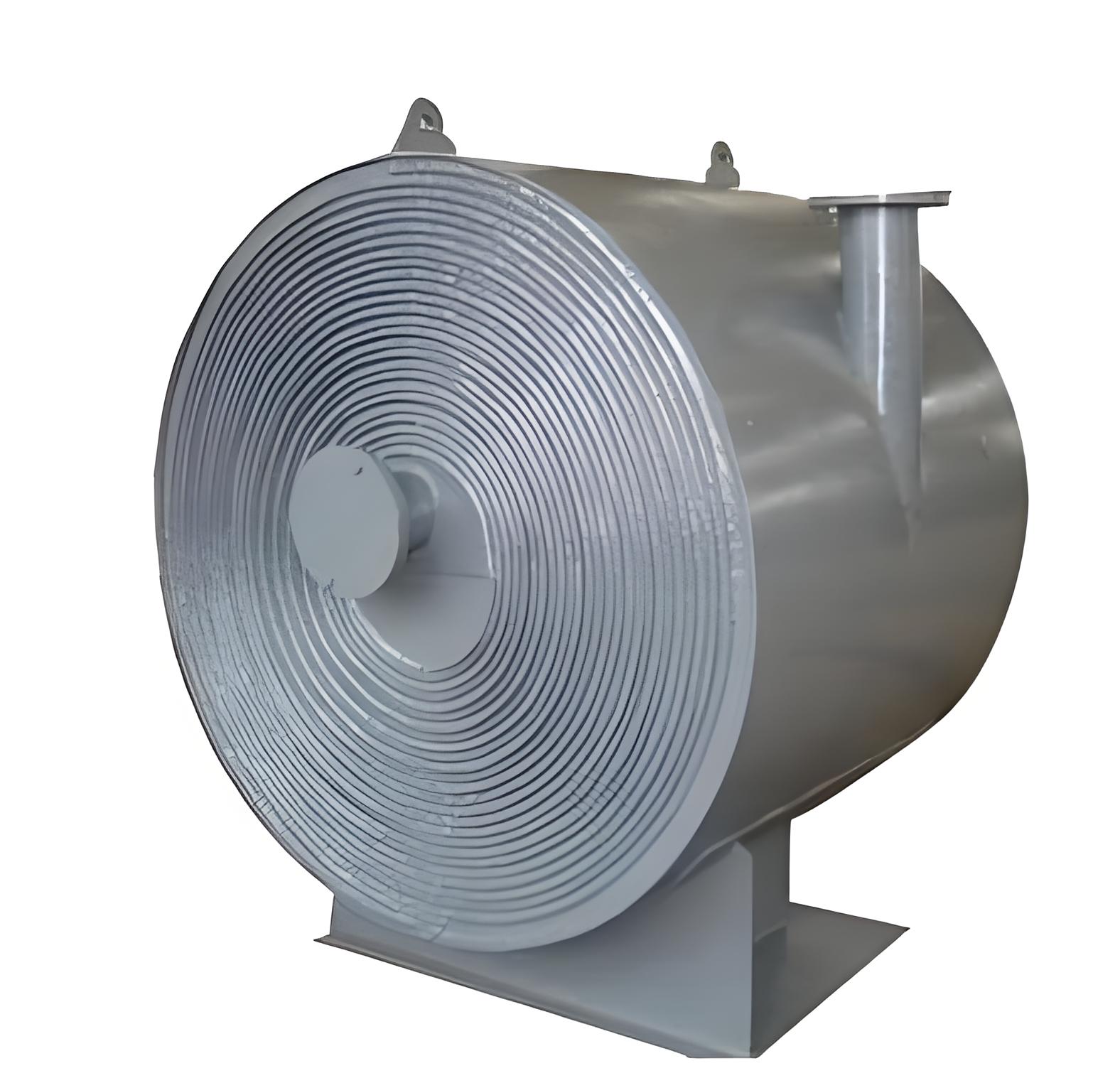
User Feedback
Customers consistently commend the SPHE for its exceptional performance and durability. Operators appreciate its ease of maintenance and ability to deliver consistent results even when handling demanding materials. Many users highlight its role in reducing operational costs by improving energy efficiency and minimizing downtime.
Frequently Asked Questions about the Spiral Plate Heat Exchanger:
- Q: How does the SPHE differ from traditional heat exchangers?
- A: Unlike conventional models, the SPHE uses a spiral plate design to enhance heat transfer efficiency and accommodate difficult-to-handle fluids.
- Q: Can the SPHE be customized for specific industrial needs?
- A: Yes, the SPHE can be tailored to meet the unique requirements of various industries, ensuring optimal performance in diverse operating conditions.
- Q: What industries benefit most from using the SPHE?
- A: The SPHE is particularly advantageous for sectors like petrochemicals, pharmaceuticals, and food processing, where efficient heat exchange is critical.