Introducing the Hot Sales Heat Exchanger Tube-U Bend Tube, an essential component for
shell and tube heat exchangers. This U-bend tube is specifically designed for various
heat exchanger type, ensuring optimal performance and durability. Our expertise in
making heat exchangers guarantees precision engineering and seamless integration into your systems. Crafted from high-quality materials, these tubes enhance thermal efficiency and withstand harsh operating conditions. Ideal for a wide range of industrial applications, our U-bend tubes are your reliable solution for efficient heat transfer.
Types of U Bend Heat Exchangers
- Fixed Tubesheet U-tube Heat Exchanger:
Description: The tubes are permanently fixed at both ends to the tube sheets.
Applications: Suitable for low-pressure and low-temperature services.
- Floating Tubesheet U-tube Heat Exchanger:
Description: The tubes are attached to a floating tubesheet that can move slightly to accommodate thermal expansion.
Applications: Ideal for high-temperature and high-pressure applications.
- Removable Bundle U-tube Heat Exchanger:
Description: The tube bundle can be removed from the shell for cleaning and maintenance.
Applications: Useful in applications where fouling or fouling is a concern.
Description: Specifically designed for condensing vapor into liquid.
Applications: Found in refrigeration systems, steam turbines, and other processes requiring vapor condensation.
- Double-wall U-tube Heat Exchanger:
Description: Features a double wall to provide additional safety and prevent leakage.
Applications: Critical in applications where contamination or mixing of fluids could be catastrophic.
Advantages of U Bend Heat Exchanger
- High Efficiency: The U-shaped tubes maximize the heat transfer surface area, enhancing the overall efficiency of the exchanger.
- Compact Design: The compact design of the U Bend Heat Exchanger allows for easy installation and integration into existing systems.
- Thermal Stress Resistance: The floating tubesheet design accommodates thermal expansion and contraction, reducing stress on the equipment.
- Durability: Constructed from high-quality materials, U Bend Heat Exchangers are designed to withstand harsh operating conditions and provide long-term reliability.
- Versatility: Available in a variety of configurations and materials, making them suitable for a wide range of applications and fluids.
- Cost-Effective: The efficient heat transfer and durability of U Bend Heat Exchangers contribute to lower operational costs and energy savings.
Material Selection for U Bend Heat Exchanger
stainless steel: Resistant to corrosion and high temperatures, suitable for a wide range of applications.
Titanium: Offers excellent corrosion resistance, ideal for applications involving aggressive chemicals.
Nickel Alloys: Known for their high temperature and corrosion resistance, suitable for harsh environments.
Copper and Brass: Good thermal conductivity, suitable for low-pressure and low-temperature applications.
Graphite: High thermal conductivity and corrosion resistance, ideal for high-temperature and aggressive environments.
Plastic and Polymer Materials: Lightweight, corrosion-resistant, and suitable for low-temperature applications.
Ceramic Materials: Excellent thermal stability and corrosion resistance, suitable for high-temperature applications.
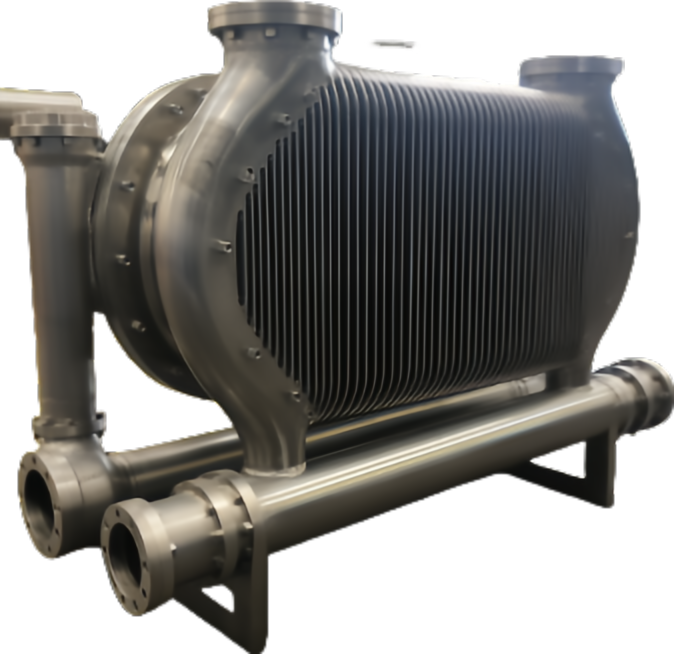
Design Considerations for U Bend Heat Exchanger
Temperature and Pressure: The design must accommodate the maximum operating temperature and pressure of the fluids.
Fluid Composition: The material selection must be compatible with the fluids being handled.
- Heat Transfer Requirements:
Heat Duty: The heat exchanger must be capable of transferring the required amount of heat.
Temperature Difference: The temperature difference between the hot and cold fluids determines the heat transfer rate.
Parallel Flow: Both fluids flow in the same direction.
Counterflow: Fluids flow in opposite directions.
Crossflow: Fluids flow perpendicular to each other.
Tube Diameter and Wall Thickness: Influence the heat transfer rate and pressure drop.
Tube Pitch: The distance between adjacent tubes affects the shell-side flow pattern and heat transfer.
Shell Diameter and Length: Determine the overall size and capacity of the heat exchanger.
Baffle Configuration: Influences the shell-side flow pattern and heat transfer efficiency.
Tube Supports and Spacers: Provide structural support and prevent tube vibration.
Tube Sheets: Must be strong enough to support the tube bundle and withstand the operating pressure.